Why Coil Width and Thickness Tolerances Matter in Precision Projects
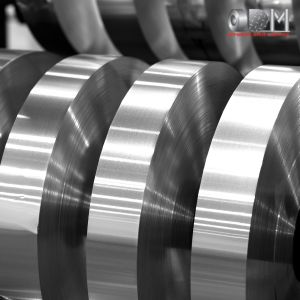
When it comes to aluminum coil processing, especially in uses that demand total precision, even small measurement deviation can create serious challenges. For aluminum extrusion companies, having consistent coil width and thickness tolerances is the key to a smooth production flow, reduced waste, and parts that meet exact specifications. Whether you're fabricating bare or painted, tight tolerance control is the difference between high-performance end-products and costly production downtime. At Offshore Direct Metals, we understand how important it is to have tight standards in coil supply, and we keep our customers ahead by delivering quality materials as specified.
Understanding Coil Tolerances
Coil width and thickness tolerances are acceptable deviations from target dimensions during coil manufacturing. In application fields where precision is paramount, such as in aerospace, automotive, or architectural uses, adherence to these tolerances is essential. For aluminum coils headed to these sectors, standard tolerances can be as tight as ±0.005 inches, depending on the target application. Standardization by organizations such as ASTM or ISO ensures uniformity and helps maintain quality from batch to batch.
The Role of Tolerances in Precision Projects
Tolerances are more than just figures on a spec sheet; they directly affect the performance and processability of materials. Inability to control tolerance in painted aluminum coils can lead to misalignment during forming, uneven finish, or mechanical issues in assembled components. For producers of aluminum extrusions, variable thickness can impact die performance, dimensional accuracy, and structural integrity of extruded parts. Tighter tolerances, on the other hand, guarantee compatibility with automated equipment, reduce tooling wear, and maintain product consistency through large production runs.
The Cost of Getting It Wrong
When tolerances fall outside acceptable specs, the consequences are real: reworks, wasted material, machine adjustments, and missed deadlines. On projects where aluminum coils are slit or formed before extrusion, even minor variations can cause whole batches to be rejected. For businesses that deal with painted aluminum coils, appearance defects such as striping, cracking, or delamination can occur when materials are not consistent in thickness. Aluminum extrusion companies are also at risk of customer dissatisfaction and contract penalties due to dimensional variation.
How Tolerance Control Impacts Profitability
Tight tolerance control adds value up front by minimizing defects, increasing yield, and improving part performance. Instead of dealing with rejected parts or production downtime, your process flows smoothly. This is particularly important for aluminum extrusion companies with tight schedules and customized product specifications. When dealing with painted aluminum coils, accuracy also guarantees uniform surface treatments and coatings, minimizing visual defects and improving product aesthetics. Offshore Direct Metals supplies materials processed using modern slitting and levelling machines, guaranteeing the tolerance precision your project requires.
What to Search for in a Coil Supplier
Not all suppliers can handle tight tolerance demands. Look for coil processors with good quality programs, in-line measurement systems, and the ability to certify the specifications of each coil. When purchasing bare or painted aluminum coils, ensure that your supplier understands the downstream implications of poor control of tolerances. Aluminum extrusion companies should also prefer suppliers that offer custom coil processing relative to their dies and production equipment. Offshore Direct Metals is proud to provide precision slitting, coating, and logistics services to keep your projects on spec and on time.
Precision Matters – Don't Compromise
When your project demands performance, accuracy matters. Correct coil width and thickness tolerances avoid costly delays, improve product quality, and allow you to maintain your reputation. Offshore Direct Metals delivers the quality manufacturers trust every time, from high-spec aluminum coils to custom finished painted aluminum coils. Call us today to learn how we can support your next precision manufacturing project.